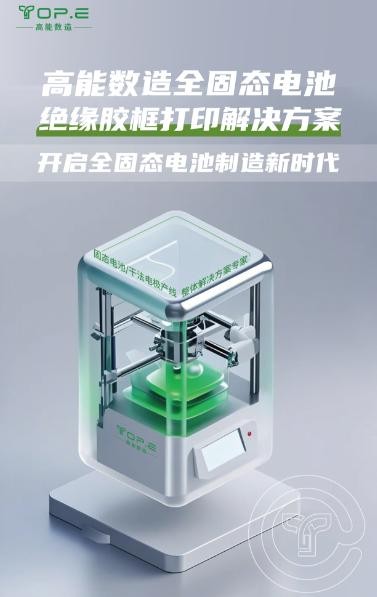
技术背景
传统湿法电极制备工艺的局限:传统的湿法电极制备工艺需要使用大量的溶剂来溶解粘结剂和分散活性物质,后续还需要复杂的干燥工序来去除溶剂。这不仅增加了生产成本和能源消耗,溶剂的使用和处理还会带来环境污染和安全隐患。
新能源产业发展的需求:随着新能源汽车、储能等领域的快速发展,对电池性能和成本提出了更。高的要求。需要开发一种更加高效、环保、低成本的电极制备技术,以满足大规模生产高性能电池的需求。干法电极纤维化技术应运而生,它为解决传统湿法工艺的问题提供了一种有效的途径。
技术原理和作用
该技术主要是利用了可纤维化粘结剂(PTFE)在特定条件下的形变特性。将电极活性物质、导电剂和可纤维化粘结剂混合在一起,通过高速剪切、加热等工艺手段,使粘结剂在剪切力作用下发生线性形变,形成纤维状结构。这些纤维状的粘结剂相互交织,形成三维的网络结构,从而将电极活性材料和导电剂颗粒均匀地包裹在一起,最终通过热压等工艺形成自支撑的电极膜和电解质膜。
材料原纤化过程
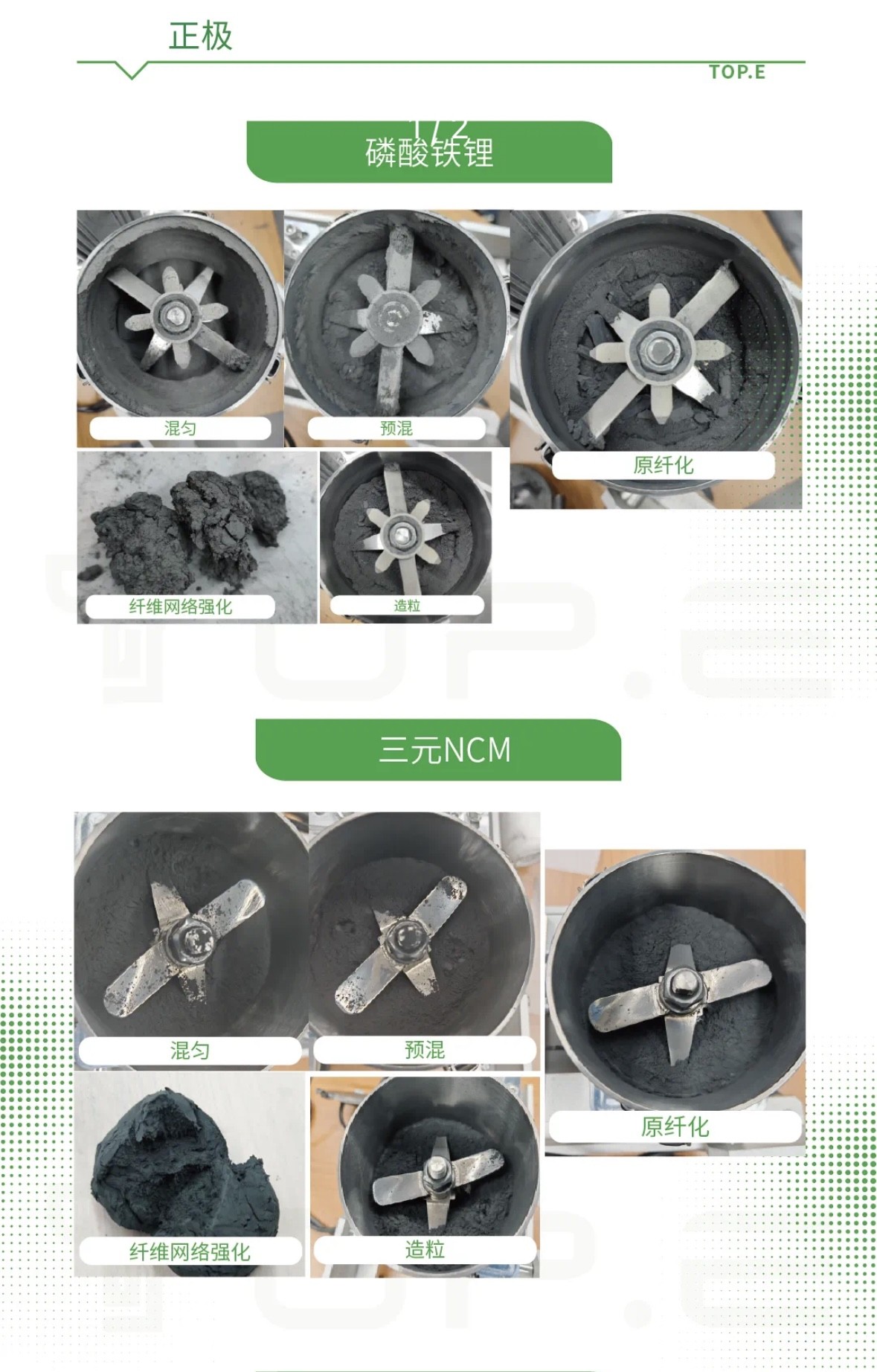
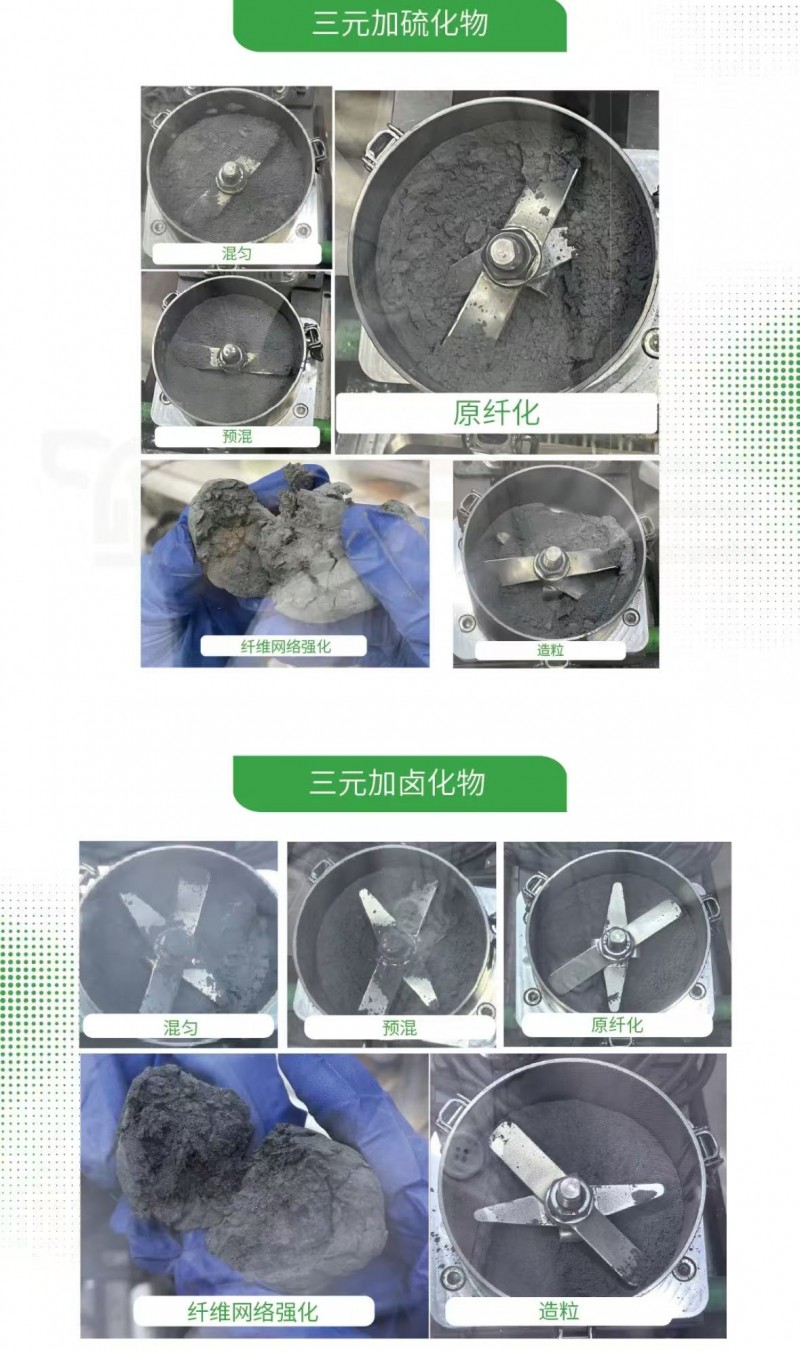
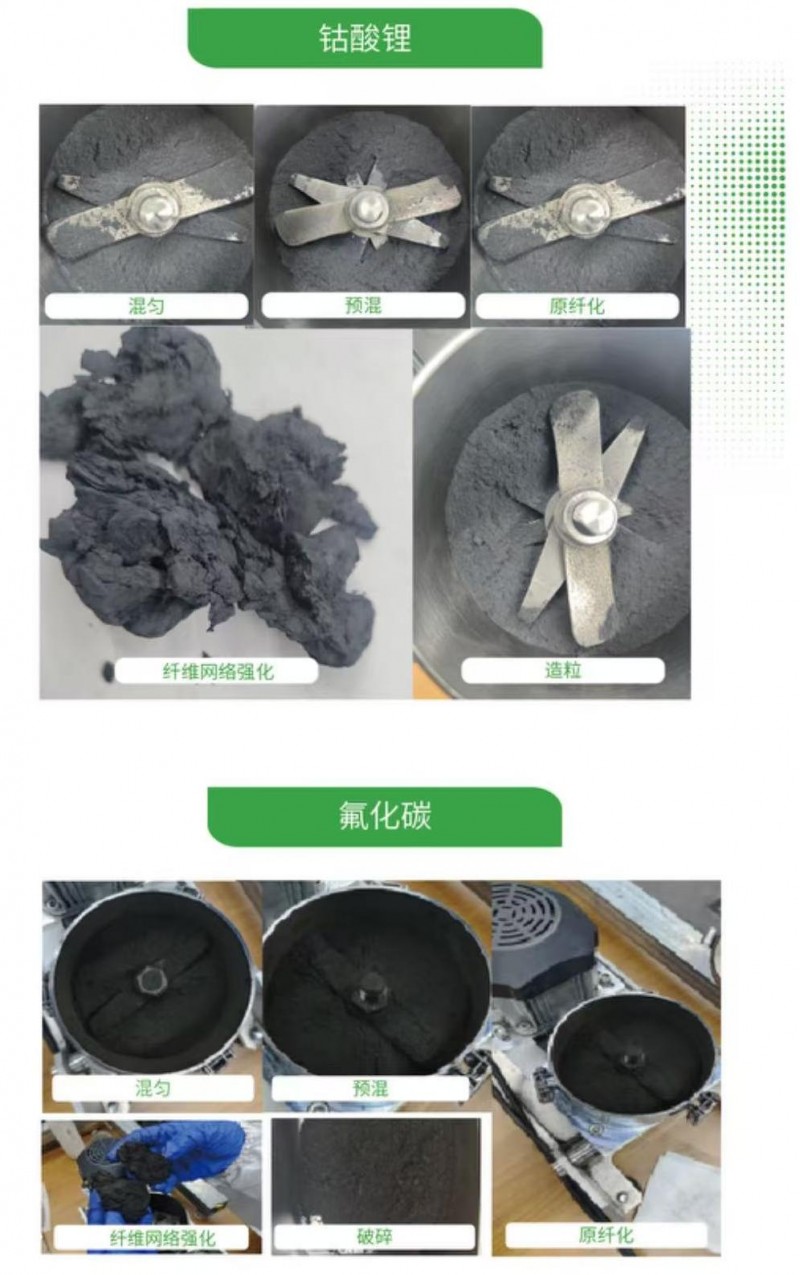
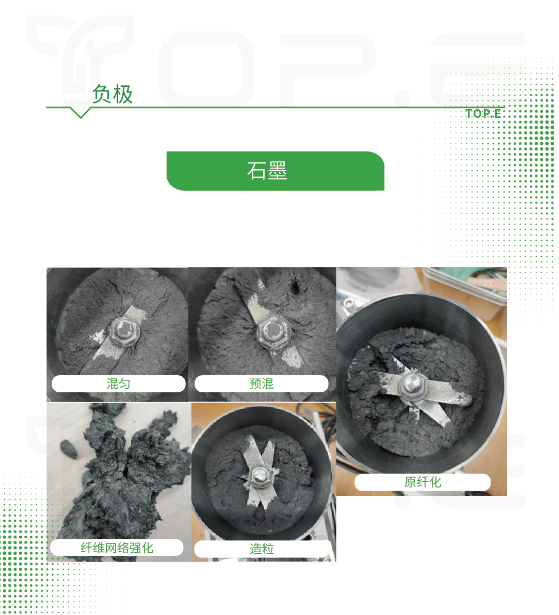
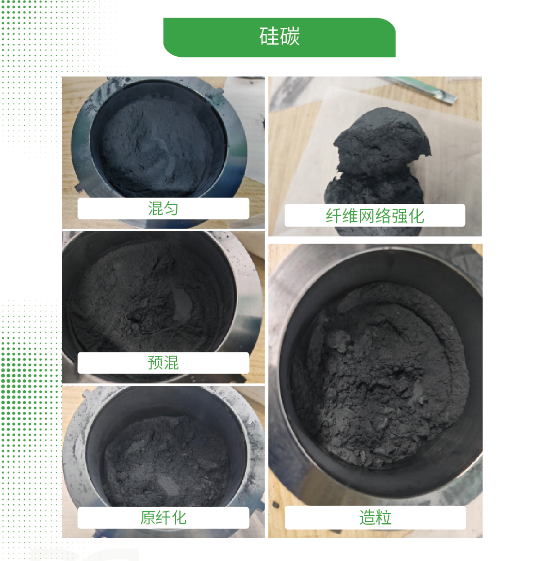
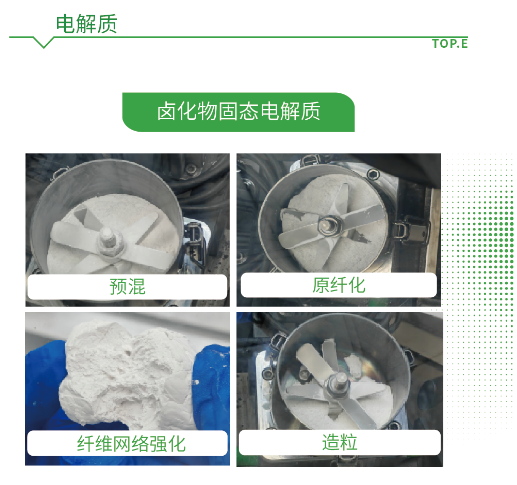
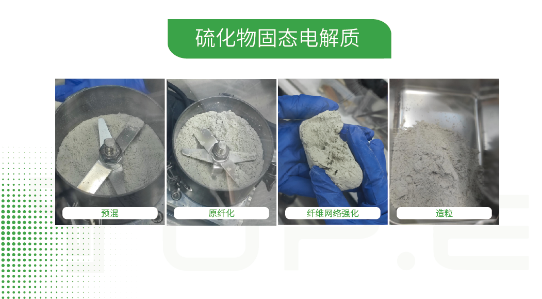

5L原纤化设备
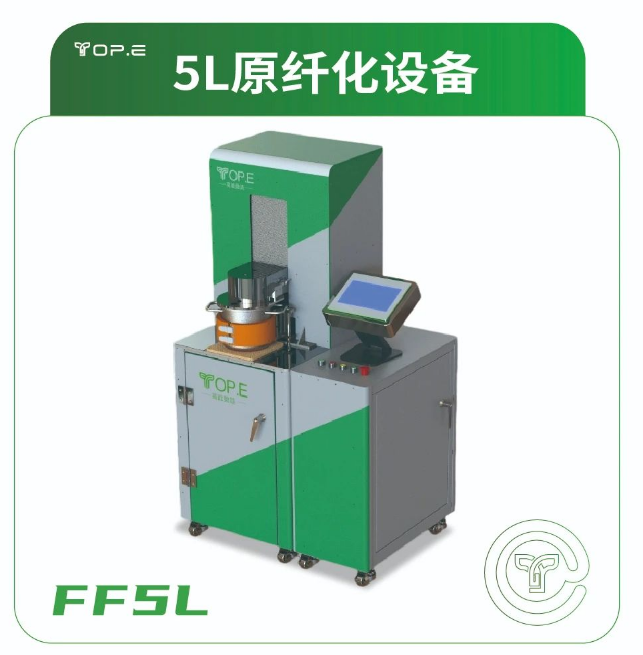
·5L小型化料罐设计,节约用料,满足实验对少量材料的要求转速实时显示可调;
·可根据工艺调整转速,实现低速均匀混料,高速剪切高效纤维化;
·叶片可更换,根据不同材料及工艺更换不同形状叶片;
·密封性能良好,避免微粉颗粒进入污染电机;
·与材料接触部分材质均为不锈钢,耐酸碱腐蚀,方便上下料。
230L原纤化设备
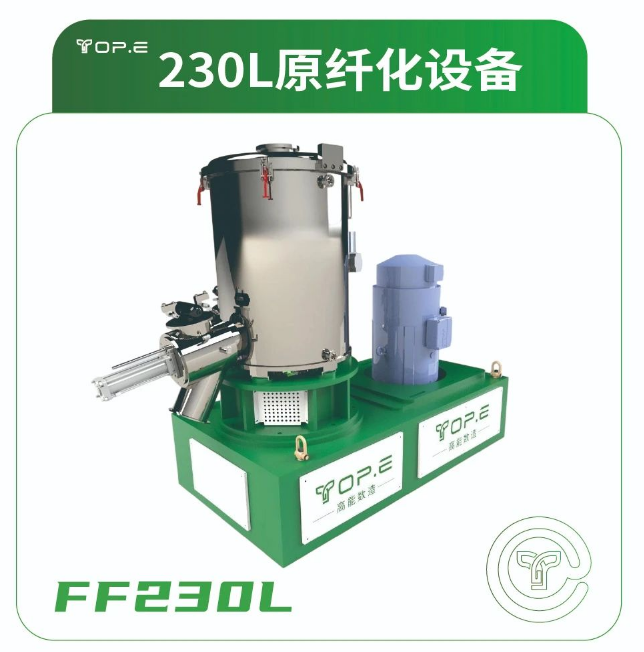
·适配百兆瓦级干法电极中试线,专门针对正极、负极和电解质等材料进行高质量混匀及纤维化处理;
·集成高精度测温、控温、罐体气氛保护功能,搭配多投料口设计,可适配多种材料同时投料;
·配备自动出料口,可衔接上下游工艺,实现纤维化工艺的自动化;
·罐体采用循环流道设计,可准确控制物料及环境温度;
·独特的轴系密封结构,避免粉料对轴承等部件的污染,提高使用寿命;
·高压反吹等配套机构,实现罐壁自清洁,高速排料等功能;
·与材料接触部分材质均为特殊镀层合金,可根据需求制作涂层,增加耐磨防腐性能。
高能数造干法纤维化技术优势
原纤化快速且均匀
高能数造干法电极原纤化采用高硬度合金刀头,经特殊处理,耐磨高强。多角度切削刃,形成循环涡流,360度搅拌,效率提40%+。
工艺控制精准
设备搭载智能传感系统,配备高精度温度传感器和转速传感器,可实时采集设备运行过程中的各项关键参数,确保数据的及时性与准确性。保证每一次原纤化过程都严格遵循最优工艺路线,有效降低次品率。
材料适配性强
设备刀头快换设计,5分钟内可完成刀头的拆卸与安装。根据不同软硬材料搭配有不同刀头,满足多样生产需求,真正实现对各类电极材料的完美工艺适配。
精确的温度控制
双温区独立控温,高精度传感器测温±0.1℃。模糊 PID 算法控温,根据反应进程动态调整温度,促进纤维的有序成型,关键环节按预设曲线梯度变化,改善电极材料结构,显著提升电极的电化学性能。
造粒高效均匀
定制造粒刀头,精准切割。成品粒度流动性优,不仅使后续的电极成膜制备更加便捷高效,还能使电极成膜及复合过程中做好更薄、更均匀,有效提升电极的能量密度与倍率性能。
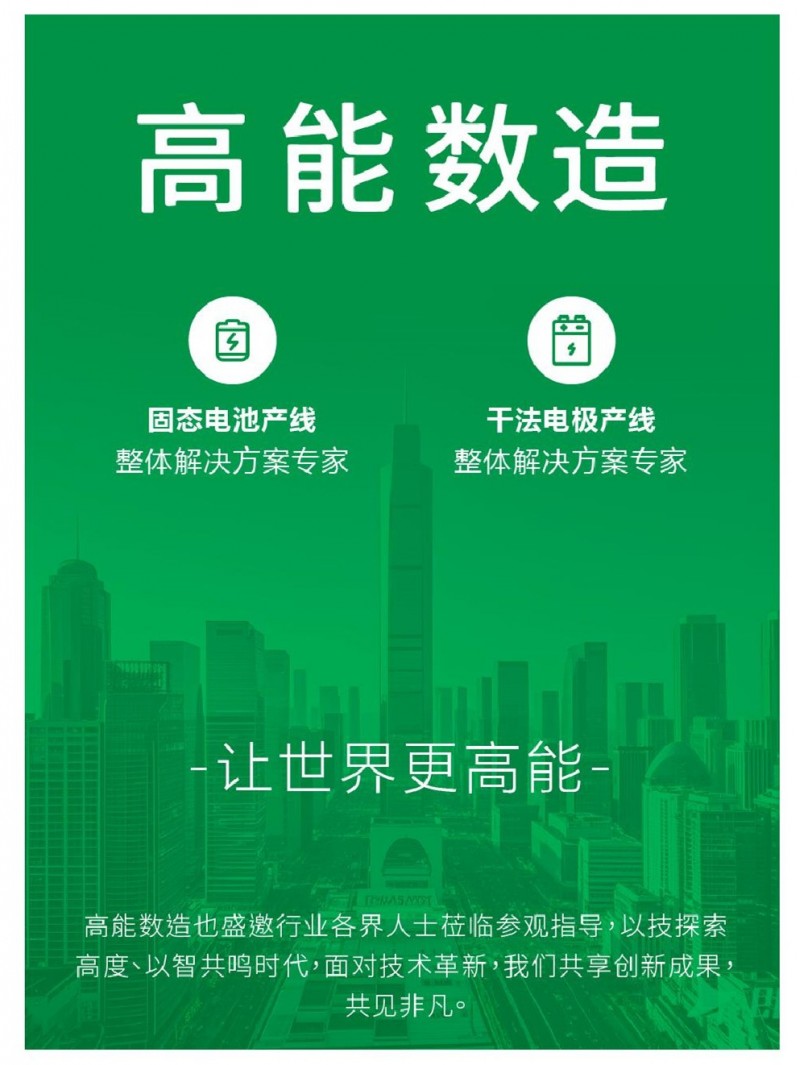
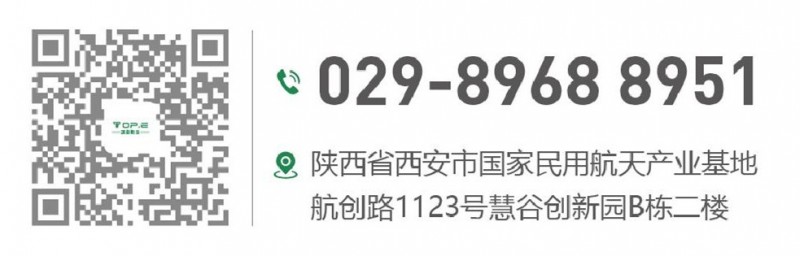