全固态电池,因其超高比能、本征安全的优势,成为了突破传统液态电池技术桎梏、开启可持续能源高效运用的 “金钥匙”
高能数造(西安)技术有限公司自创立伊始,便以 “让电池更高能·让产品更高能” 为使命,致力于开发先进的固态电池与干法电极产线整体制造解决方案,以前瞻的战略眼光和深厚的技术底蕴,获得了全固态电池与干法电极智造领域产业用户的关注与认可。
作为国家级高新技术企业,高能数造现已获得宁德时代、中国一汽、东风汽车、中科固能、潍柴动力等国内头部锂电企业、新兴固态电池企业及头部新能源整车企业产线设备订单,正稳步践行“赋能客户实现固态电池与干法电极产业化智能制造” 的产业承诺。

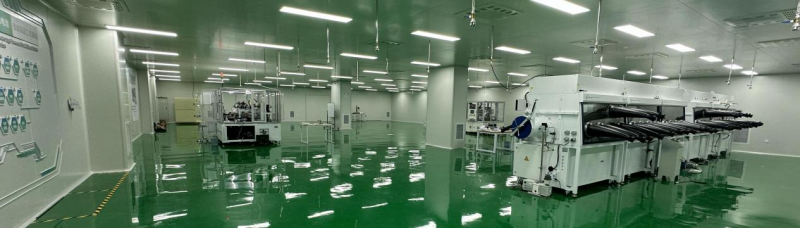
高能数造汇聚多方智慧,与国家石墨烯创新中心、中科固能、北京理工大学、西安交通大学联合成了实验室,基于联合实验室的创新成果,我们能够为目标客户提供涵盖技术研发、工艺设计、设备制造、产线搭建及后期技术支持的固态电池与干法电极产线整体解决方案。
其中,高能数造与国家石墨烯创新中心共建的固态电池3D打印工程技术中心,已建设完成方形铝壳动力电池试验线、软包及圆柱电池试验线、固态电池3D打印试验线、石墨烯涂层集流体试验线等先进智造产线,整体产线占地面积超过5900平方米,具备固态电池、先进储能电池、新型动力电池、3C锂电池、干法电极的测试分析、研发试制与小规模量产能力,可提供方形铝壳电池(100Ah以上)、全极耳大圆柱电池(32140/4680/4695)、软包电池(2-100Ah)、固态电池的制作和中试生产服务。
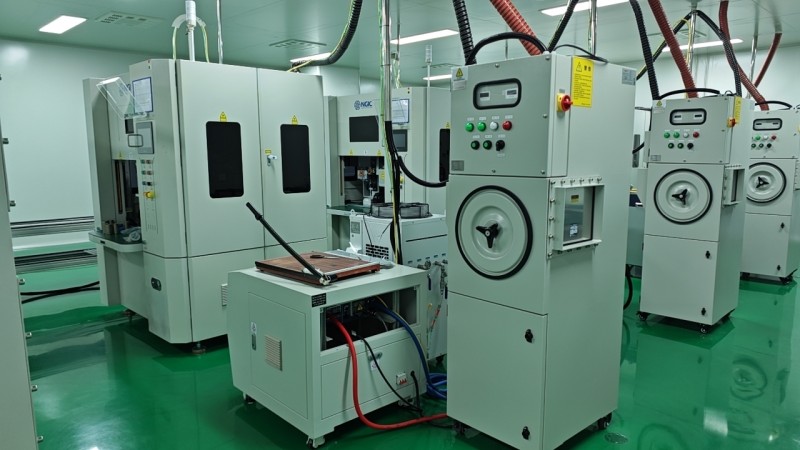
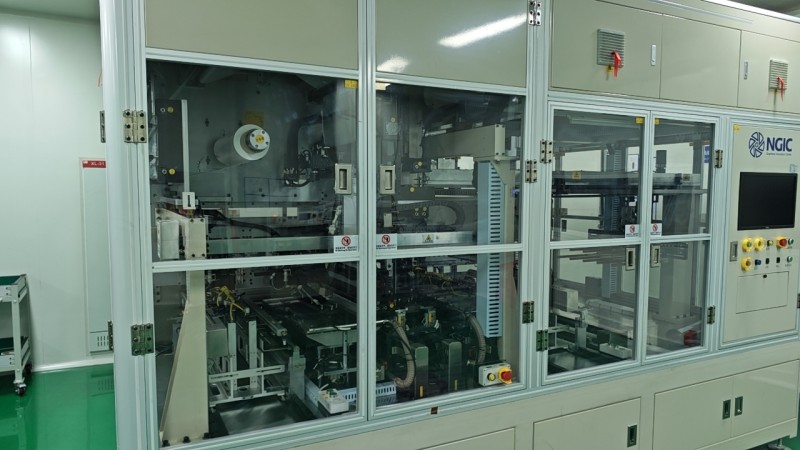
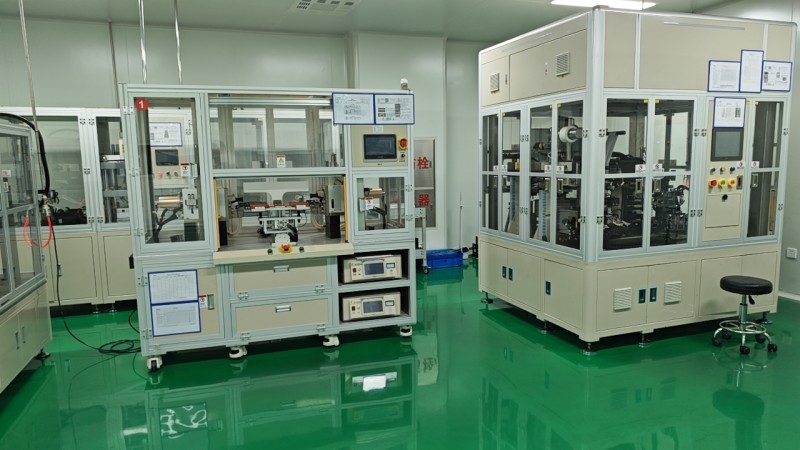
锚定核心赛道,驱动产业革新
高能数造始终将目光聚焦于 “固态电池”与“干法电极”两大核心领域,矢志打造全球领先的新能源智造生态,在智能制造产线整体解决方案的技术高地持续深耕。
在固态电池产线领域,高能数造精准把握新能源企业从研发到量产过程中的痛点,凭借全固态电池一体化智造等核心技术,为客户提供从实验室研发到规模化生产的全链条智造装备与整体产线解决方案。
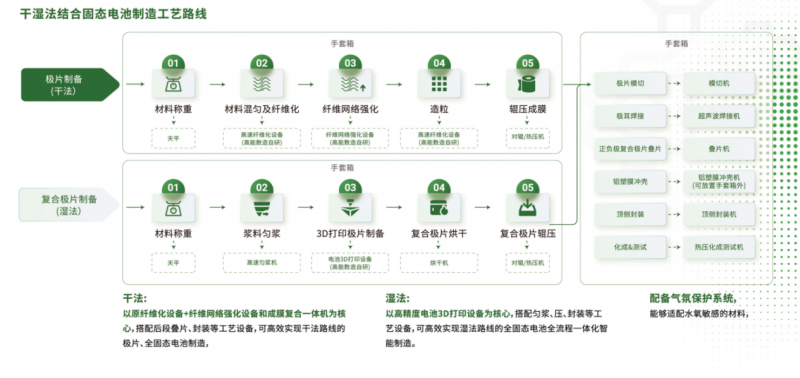
全固态电芯一体化制备技术
高精度3D打印技术结合智能制造工艺,实现正极-电解质-负极的连续叠层制造。改善正负极与电解质间固固界面相容性,确保离子在正负极和电解质间的有效传输。有效降低界面阻抗,提高电池循环稳定性和充放电效率。
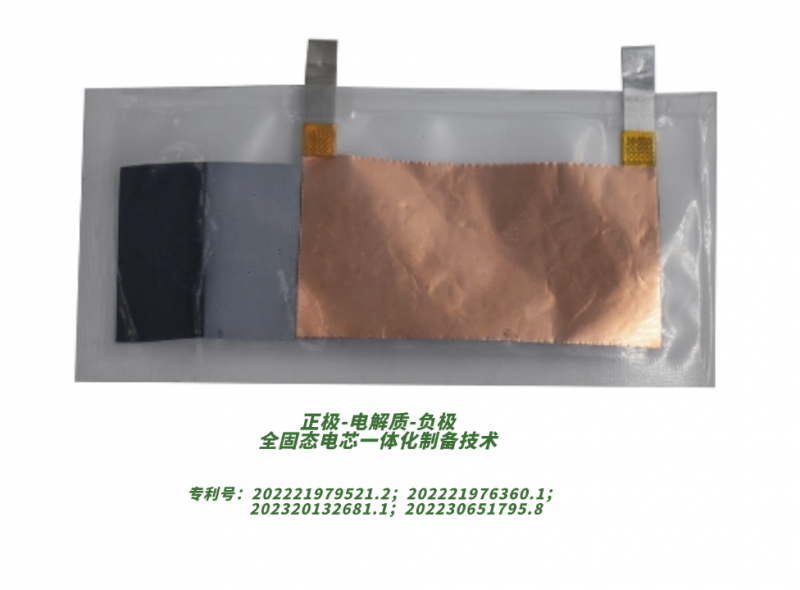
超薄复合固态电解质膜制备技术
高能数造高精度3D打印(原位层叠)技术能够解决双层及多层湿法浆料的原位制备难题,将单层或多层电解质原位连续打印在正/负极表面。有效改善正负极与电解质间原本固固界面相容性差的问题,确保离子在正负极和电解质间的有效传输,降低界面阻抗。
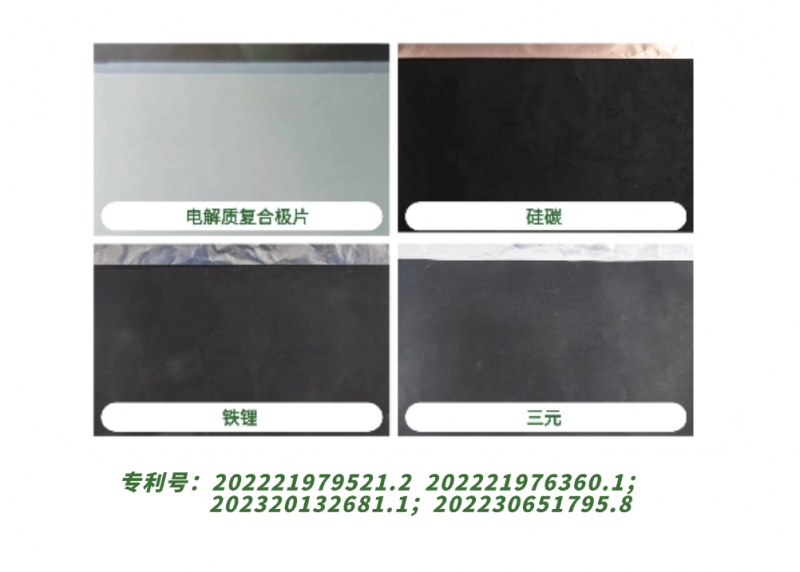
固态电池干湿结合制备技术
纯干法制备固态电池时,固-固接触的界面问题改善需要增加工艺步骤;纯湿法制备固态电池又需要考虑正负极和电解质间溶剂体系的选择问题。
高能数造开发出干湿结合的制备工艺技术,可使用干法制备正负极,湿法打印电解质,此工艺技术路线既能在电芯制备阶段改善正负极与电解质的界面问题,又能避免正负极和电解质的溶剂选择冲突。
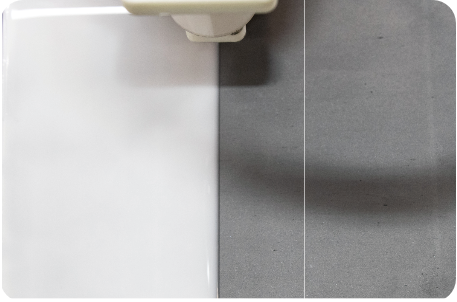
硫化物全固态电池干湿结合制备技术
对于无法确定湿法硫化物卤化物溶剂体系的客户,高能数造开发了专门用于制备全固态电解质膜的干法技术及相应设备,可实现各种电解质膜的干法连续制备,省去了粘结剂和溶剂体系的开发工作,且能更好的发挥卤化物与硫化物的高离子导。
对于已确定湿法硫化物和卤化物溶剂体系的客户,高能数造的高精度湿法3D打印技术可实现大幅面,超薄的电解质膜原位制备,改善正负极和电解质层间的界面接触,保证正负极与电解质间的离子传输,降低界面阻抗,提高电池的循环稳定性。
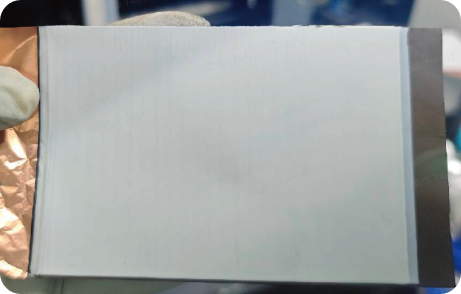
固态电池材料体系全适配
高能数造高精度湿法3D打印技术已实现超薄聚合物电解质膜(10微米以下)、复合电解质膜(20微米以下)以及硫化物电解质膜(30微米以下)的打印制备。
高能数造干法电极技术已实现氧化物、卤化物以及硫化物 电解质膜的干法连续制备,提高生产效率的同时使得卤化物、硫化物等高离子导电解质材料的性能得以充分发挥。
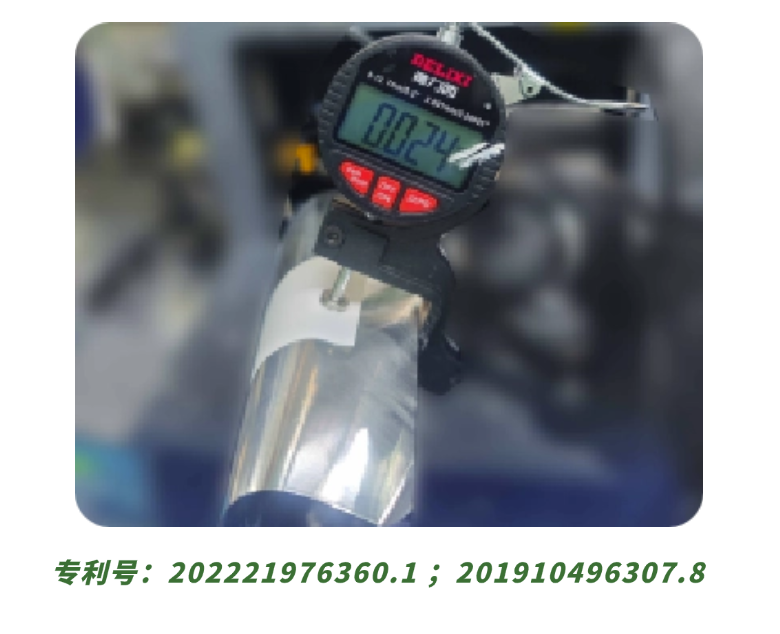
锂金属负极制备技术
锂金属具有高达 3860mAh/g 的理论比容量,远远高于传统锂离子电池中常用的石墨负极材料(372mAh/g),这意味着在相同质量的情况下,锂金属能够存储更多的电量,从而可以显著提高电池的能量密度。但在实际应用过程中,锂金属由于本身机械强度差、易粘连等问题、极易出现破损、导致其应用受到限制。高能数造针对锂金属的实际使用问题, 开发了锂金属负极成型机,通过设计自动化流程及开发特 殊的转运机构,解决了以上难题,让锂金属能在锂离子电池产线中投入使用。
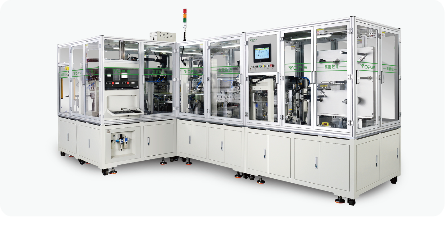
全固态电池致密化技术
在氧化物、卤化物和硫化物体系干法全固态电池中,固-固界面相容性差的问题非常显著,正负极与电解质之间的不良的界面接触无法确保离子在电极与电解质之间的有效传输,可能造成空隙或物理剥离,导致电池循环的稳定性差、充放电 效率降低。高能数造针对此问题开发了电池致密化技术,可有效改善正负极与电解质间的界面接触,解决上述问题。
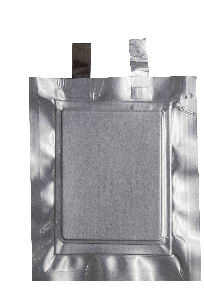
固态电芯热压化成技术
全固态电池的固-固界面相容性差的问题非常显著,虽然在电芯制备阶段可利用致密化工艺改善,但电芯的测试阶段由于正负极材料会发生一定的体积变化,会造成界面脱离, 导致电池性能迅速衰减。高能数造开发了针对固态电池的热压化成技术,在测试阶段可以提供稳定且平衡的压力,抑制正负极的体积变化,维持材料间的界面接触,保证电芯循环的稳定性。
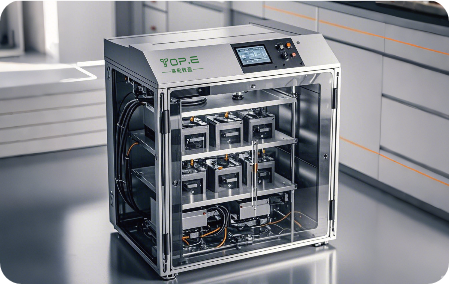
固态复合极片绝缘框制备技术
固态电池中有等静压工艺步骤,在极片堆叠后的等静压阶段,电解质膜由于受到外部压力以及极片间相互作用力,于正极边缘区域极易产生翻折现象,会破坏电解质膜的结构完整性,致使电解质膜断裂、电芯短路。高能数造为了解决此问题,开发了复合极片绝缘框的制备技术,使用高精度的打印设备,将封边材料均匀地打印在正极材料的周围,确保每一处都能被封边材料完全覆盖,不留任何空隙和高度差。杜绝等静压工艺步骤中的翻折现象。
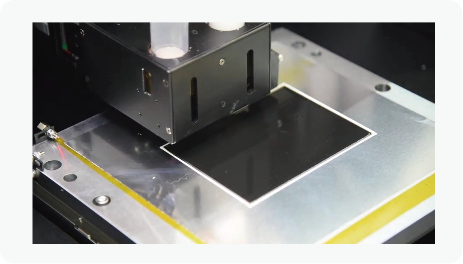
无隔膜叠片技术
全固态电池中没有隔膜,所以目前的叠片设备和技术都不 适用。此外,聚合物基的复合电解质容易产生粘连现象,影响复合极片的转运,降低电芯良品率。高能数造根据此工艺问题,开发了新的自动化流程以及特殊的转运机构,解决了上述问题,实现固态电池叠片工艺和技术的全适配。
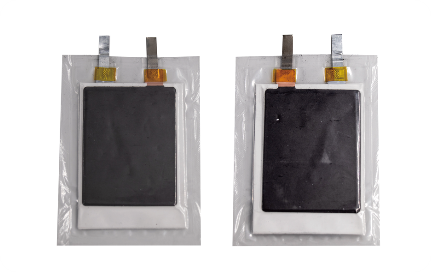
在干法电极产线方面,高能数造凭借自主研发的高品质原纤化等干法核心技术,实现生产全流程精细化管控。从原材料超高效均质处理到电极高品质连续制造成型,每一道工序都历经数百次的技术迭代与优化,确保产出的干法电极在基础性能、一致性和稳定性上达到行业顶尖水准,为新型高性能电池提供更加先进的智造解决方案。
干法电极高品质原纤化技术
高能数造通过对不同材料粒径与密度的仿真分析,研发出适配不同材料的不同叶片,保证在高速旋转过程中提供强 有力的剪切力,通过设备的精确控温,保证粘结剂在可以纤维化的适宜温度区间内,以达到材料最大程度的原纤化。同时纤维网络强化设备可以进一步提高纤维化的效果和强度,增加极片的机械性能和生产效率。连续化的生产设备与工艺流程,可以满足干法电极高品质的量产。
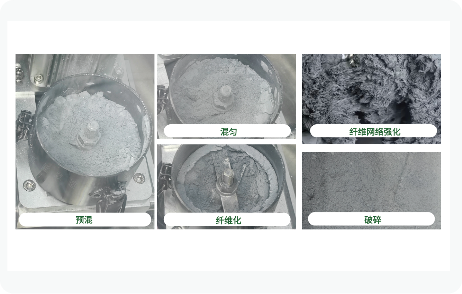
干法电极高品质制膜复合技术
高能数造自主研发了自动化连续投料设备,配合多级差速辊,可实现制膜减薄一体化作业,减少设备和场地投入。多级连续减薄步骤,设备可输出厚度与面密度均一性较高的极片。通过大吨位的压延复合一体机,配合高精度的纠偏与厚度传感器,实现膜材与集流体的双面复合,并进一步提高干法极片的面密度。
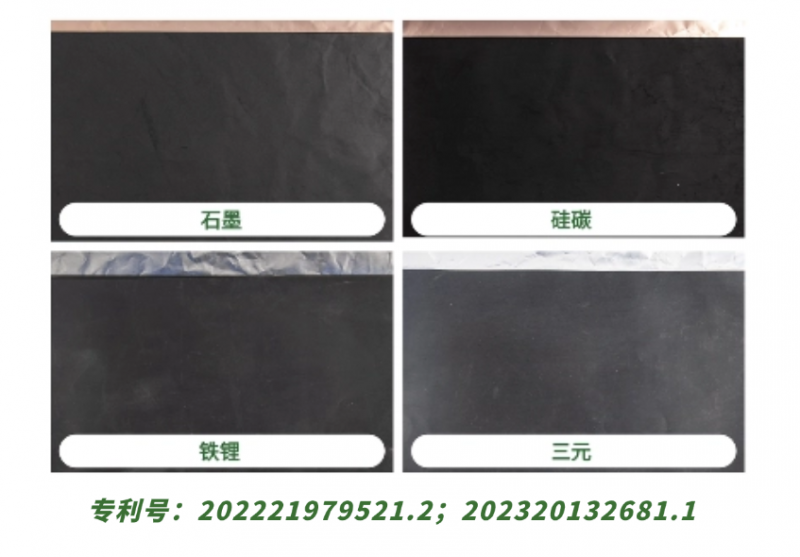
纳米硅负极制备技术
纳米硅负极由于其密度小,质量轻,比表面能大,易团聚,在干法技术中会遇到和粘结剂材料难以分散均匀以及不易使 PTFE发生纤维化等问题,高能数造针对这些问题,特别设 计了定制化的刀头,开发了独特的纤维化工艺,能够完成纳米硅负极的干法膜连续制备,使纳米硅材料在电池中的应用向前迈进了一大步。

多种干法电极专用材料体系储备
在粘结剂方面,高能数造和大金氟化工深度合作,开发出可改善极片拉伸强度、优化负极应用的粘结剂方案。
在集流体方面,高能数造采用干法专用集流体,可有效增加自支撑膜粘附力,提高极片剥离强度。
在导电剂方面,高能数造和国家石墨烯中心深度合作,开发针对干法工艺的高效导电剂,提升极片电导率的并获得更优机械性能。
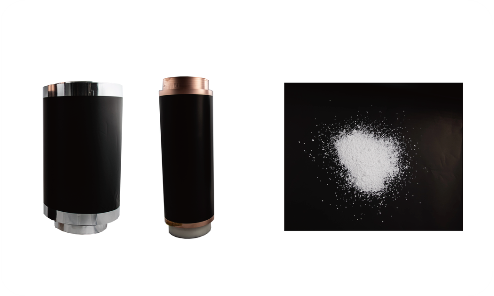
此外,得益于丰富的行业经验与技术沉淀,高能数造现已能为客户提供涵盖【产线规划方案】、【产线工程方案】、【制造工艺方案】、【核心设备定制方案】、【电芯设计方案】、【电芯试制方案】、【材料体系方案】七大核心领域业务,全面助力固态电与干法电极产业化加速落地。
高品质核心装备,赋能产业腾飞
全固态电池产线整体解决方案:产线级装备
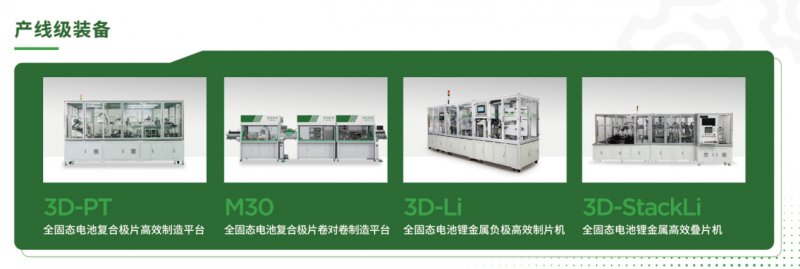
干法电极产线整体解决方案:产线级装备
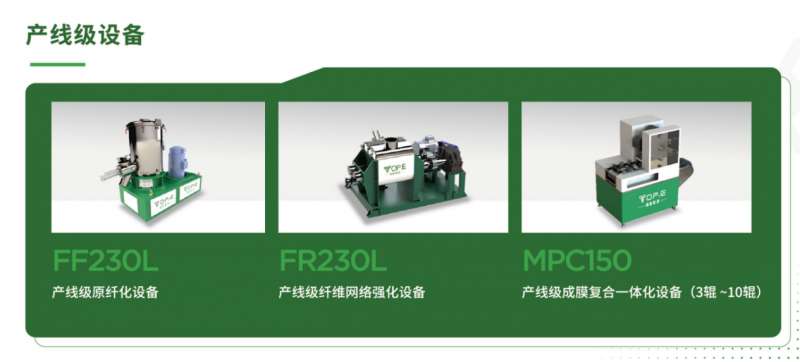
携手同行,共筑能源新未来
在新能源产业蓬勃发展、竞争日趋激烈的当下,高能数造不仅是新能源企业值得信赖的合作伙伴,更是产业创新升级的坚定同行者。我们深知,每一次技术突破都在为人类迈向清洁能源时代添砖加瓦;每一套智造装备的交付,都在为全球能源转型注入强劲动力。
秉持“让世界更高能”的愿景,高能数造愿与全球新能源伙伴并肩携手,以创新为引擎,以技术为羽翼,共同书写新能源产业高质量发展的壮丽篇章,为实现全球碳中和目标、构建永续发展的绿色世界贡献中国智慧与中国力量!
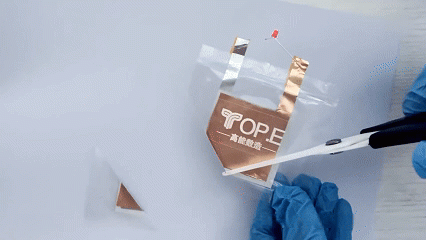
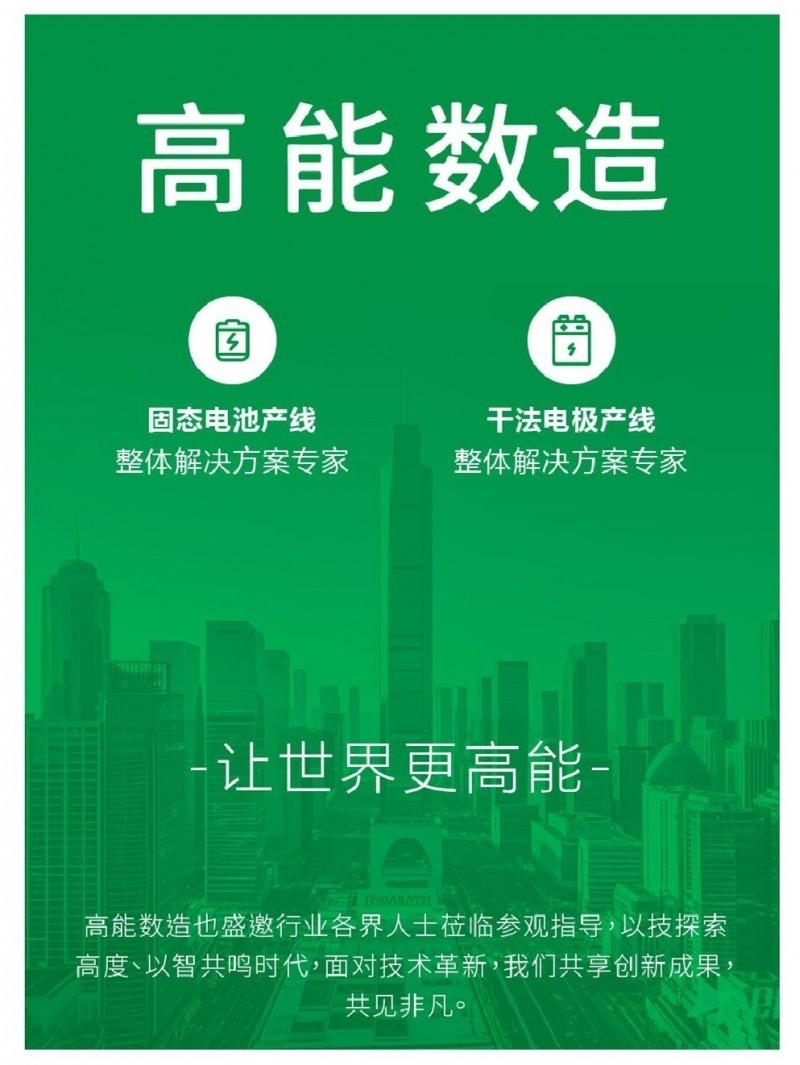
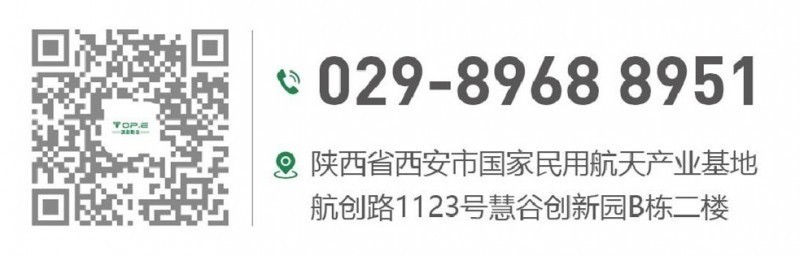