2019年4年,远景集团宣布完成收购AESC,并基于AESC原有团队和体系成立了远景AESC。远景AESC,除了在产品设计上下功夫之外,在工程能力的积累也是保证日产Leaf零事故的重要原因。
远景集团CEO张雷,曾在两会上提出加强动力电池安全标准的指定,也在2019年达沃斯论坛上表达了更多远景集团对于动力电池安全性的重点工作。
文章原载@高工锂电赵冲
“电动化、智能化、网联化、共享化”的叠加融合、相互赋能,推动着汽车产业迎来百年未有的大变革。
在这场变革中,电动化是第一步。就在刚结束的2019世界新能源汽车大会上,全球汽车产业主要相关方达成了博鳌共识:力争到2035年全球新能源汽车的市场份额达到50%,全球汽车产业基本实现电动化转型。
要实现这样的目标,从动力电池的角度来看,信心与挑战共存,一方面,包括能量密度、寿命、快充、低温等核心性能指标正在被逐个攻破,足以支撑起电动车性能超越传统车。
但硬币的另一面是,频繁发生的电动汽车安全事故,已经成为电动汽车走向市场化的“阿克琉斯之踵”,2019年以来,包括蔚来、特斯拉等明星车企频繁发生的电动汽车安全事故引发了消费者的恐慌与担忧。
“安全事故已经成为当前新能源汽车发展的致命隐患,必须尽快解决。”
中国科学院院士、清华大学欧阳明高教授表示,长期来看,安全既是影响电动汽车可持续发展的生命线,也是市场竞争和品牌塑造的一个主旋律。新一代电动汽车不是靠动力性,而是要靠安全性。谁安全可靠,让用户放心,谁将来才能赢得客户。
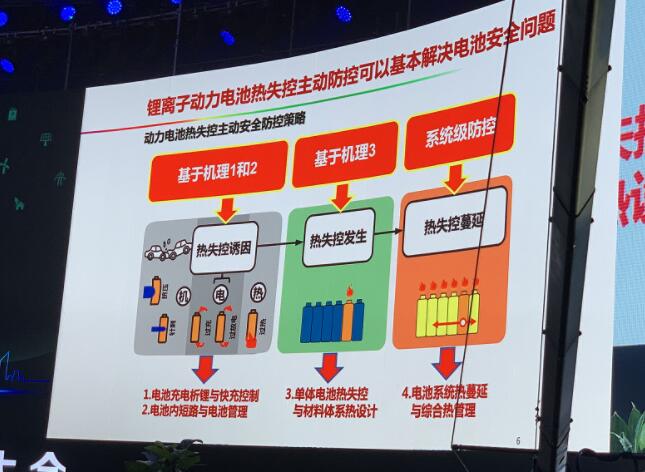
图片来源:欧阳明高演讲PPT
他山之石,可以攻玉。在2019世界新能源汽车大会上,包括欧阳明高、宁德时代董事长曾毓群等在内的多位学术界和产业界领袖都提将日产Leaf车型作为电动汽车安全的典型案例被多次提及,并呼吁产业链企业学习借鉴其在安全设计和防范上的经验。
被当做标本被反复提及,这与日产Leaf推出9年来在全球打造的零安全事故记录密不可分。
日产汽车副社长坂本秀行在大会上介绍,截至目前,日产Leaf全世界卖了41.5万台,单台车有288个电芯,单车装载电量60kWh,加在一起超过8000万个电芯,目前保持了零事故的记录。
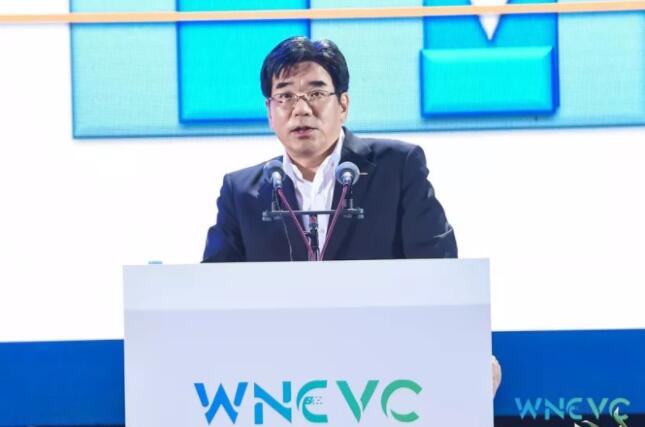
日产汽车副社长坂本秀行
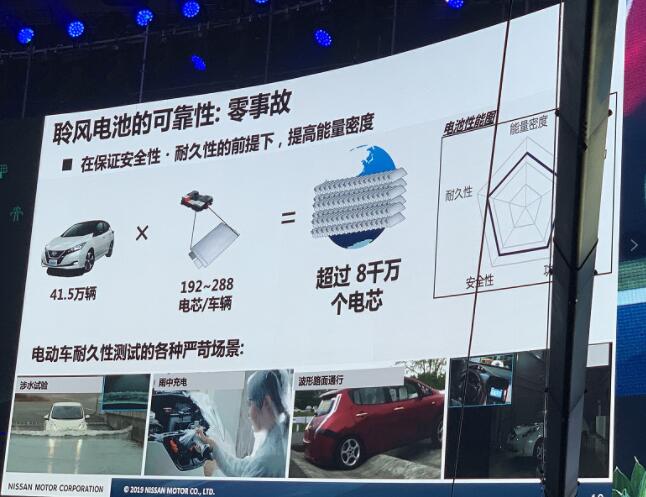
图片来源:坂本秀行演讲PPT
电动汽车领域资深从业者朱玉龙也证实了坂本秀行的介绍,他曾专门检索统计过日产Leaf的安全事故,在公开的检索中的三起事故中,主要都是外部因素(地震、山火、充电桩起火)引发,但即便是在如此剧烈的外部环境下,其动力电池系统都没有出现燃烧起火。
零事故背后,是日产及其动力电池供应商对于在安全上的出色把控。
坂本秀行坦言,日产在经过了长时间的电池研究之后发现,实现电池能量密度的提升其实并没有那么难,难点在于保障电池的安全性,这也是日产开发电动汽车时最为重视的一点。
2007年,日产汽车与NEC集团成立合资公司AESC,主要目的就是结合电动化的开发需求,将NEC的电芯技术以合资的方式快速导入到电动汽车上,而日产Leaf所使用的动力电池,正是AESC所设计和开发。2019年4年,远景集团宣布完成收购AESC,并基于AESC原有团队和体系成立了远景AESC。
坂本秀行在大会接受群访时也回应,Leaf上所采用的远景AESC电池,除了在构造上与其他的电池有显著差异之外,还拥有在发生高强度剧烈撞击时的自我处理机制,以及防止劣化方面的特殊设计。
高工锂电获悉,日产Leaf所使用的电池,其在电芯、模组、BMS、Pack、整车等各个层级的设计中,都针对可能发生的安全风险,做了系统化的设计和防范。
坂本秀行介绍,动力锂电池安全防范最重要的三点分别是:如何设计电池包;如何控制电池本身的散热;如何设计失效管理系统以应对突发状况。围绕这三点,日产汽车和远景AESC共同进行了针对性的开发。
电池包的整体设计涵盖了电芯、模组、pack三个层级。在电芯环节,首先是确保化学稳定性,要选择稳定的材料,并通过上千次的各类评估来测试它的稳定性,例如过充、振动、热冲击、甚至针刺等等。
坂本秀行介绍,从电芯角度看,液态电解质和电池正负极材料的选择非常关键。同时,电芯内部的短路与隔膜材料的选择紧密相关,因此,远景AESC在电芯内部材料上都做了特殊的设计。
在模组和Pack环节,通过结构来保护电芯免受到冲击。这包括了整体外壳ip67保护设计、自然风冷散热系统、分离式充电系统设计、利用热传导使整个车身都变成电池散热体等,同时,其还充分考虑了FMEA,确保设计留安全余量。
值得注意的是,在Pack环节,除了物理上的保护措施,关键是要通过BMS对电芯模组进行故障诊断,监测异常发生,并预测可能出现的问题,从而通过断电来阻止问题发生。
高工锂电注意到,在BMS环节的保护策略上,Leaf可以说是整个行业的先行者,其通过一类/二类/三类故障的定义来对BMS检测到的故障进行分类。整体思路是,从行车的限制、充电的限制和故障显示三方面来分成四种不同的故障模式。
根据监测到的不同情况,日产Leaf上的BMS会以不同的形式来对电池系统进行防护,这包括从动力源头切断任何充电和放电的过程,主要响应比较高等级的故障;考虑电池的故障在一定范围内之类,限制电机输出功率,在充电模式下充电停止(阻止了能量回收);限制电池包的输入和输出功率。
基于BMS安全保护策略而建立的电池包失效安全系统设计,让Leaf在使用中明确了电池使用安全边界,并可以实现实时报警,从而避免了热失控发生,并起到了失效防护的作用。
根据欧阳明高团队对于动力电池热失控的诱因分析,一是由于机械变形、挤压、撕裂,隔膜破裂、极端过热等各种原因导致的内短路。这需要从上述系统本身安全性和材料体系的角度,进行单体电池热安全设计。二是过充、快充、老化电池、低温充电等导致的析锂,针对后者,则需要通过对于充电算法进行改进和优化。
而在充电算法上,日产Leaf同样做了大量的数据积累和实验,欧阳明高就介绍,其团队和日产在充电的算法上有合作,其充电算法是基于大量数据MAP图进行,通过大量实验数据支撑,使充电算法能够考虑各种各样的影响因素,这使得其避免了很多热失控问题。
高工锂电了解到,日产Leaf的充电安全管理也设置在BMS系统里,可以在充分理解及大量测试结果的支持下,定义明确清晰的充电电流电压边界,以此管控整个充电过程,保障充电的安全。
要最终达到电动汽车的安全,仅靠在产品开发设计上的投入还远远不够,还需要在生产制造环节做好把关。
可供参考的一组数据是,国家市场监督管理总局介绍,截至2019年5月,国内新能源汽车共召回12.3万辆。其中由于三电系统故障导致的召回占比为50%,在这之中设计原因占到40%,生产制造原因占到60%。
产品设计得再好,但是要稳定、高质量生产这又是另一回事,这就要求核心零部件企业需要有较高的工程能力,这里的工程能力是指生产制造和质量体系。
针对作为电动汽车心脏的动力电池的生产,高工锂电向日产Leaf的动力电池供应商远景AESC做了深入调研,详细了解了其在生产制造和质量体系的建立上如何实现安全把控。
远景AESC介绍,除了在产品设计上下功夫之外,在工程能力的积累也是保证日产Leaf零事故的重要原因。
“AESC的安全体现在它的工程能力与质量控制能力,因为脱胎于整车厂,拥有整车多年积累的工程能力,因此,我们一直严格遵循汽车行业的标准,同时,在满足汽车行业通用标准的前提下(IATF16949和VDA标准),AESC还针对动力电池设定了更为严苛的控制体系。”
远景AESC负责人向高工锂电介绍,其从项目管理控制,供应商控制,来料控制,生产过程控制和客户和市场端质量控制都有着严苛的标准和控制监督体系。
而在AESC被远景集团收购后,同样将这种严苛的工程及制造标准体系得到延续,依托于此前AESC的日本核心团队,在位于无锡江阴的中国工厂里,其整个生产制造和质量体系也在快速建立。
以生产过程为例,远景AESC做到了770多项的质量监控,每一个项目都是在一套PDCA循环中开展的。这意味着每一个控制项目都有一个团队在后面进行计划执行监控和控制。
.jpg)
图片来源:远景AESC发布会
此外,从电芯到模组再到电池包,远景AESC共设置了45个万数据采集点。仅电芯制造层面,每一块电芯就具备超过2千个数据采集点。海量的数据节点形成了远景AESC独有的可追溯管理系统,这套系统收集并监控大量工艺及电池状态参数。
这些数据和其从前端客户那里收集到的数据形成一个闭环,这样可以帮助电池设计留更精准的余域,远离安全极限状态,在此基础上制定更为精准的BMS控制策略。
在标准化制造上,远景AESC于2010年建厂之初就实现完全标准化运营生产,在2012年,远景AESC将这套技术和生产流程转移至海外,在美国、英国设立电池生产基地,保证生产出相同品质、相同产品性能的电池产品。
在供应商选择及采购环节,远景AESC也始终将安全和质量放到第一位,而没有一味追求成本,对此,其思路是,过度追求成本可能反倒会带来巨大的成本投入。
以此次蔚来召回为例,共召回电动汽车4803辆,根据行业平均值来算,其单车电池成本可能在8——9万元,这意味着,仅在动力电池方面的花费预计在3.84亿元以上,再加上其他费用,业内保守估计,此次召回整体成本将超过5亿元。
而更为巨大的损失是召回带来的品牌影响,远景AESC上述负责人坦言,配套日产Leaf8000万个电芯零安全事故其实也是一种品牌价值,远景AESC的愿景之一就是,继续延续在动力电池零安全事故,助力除了Leaf之外的更多品牌电动汽车实现“极致安全”。